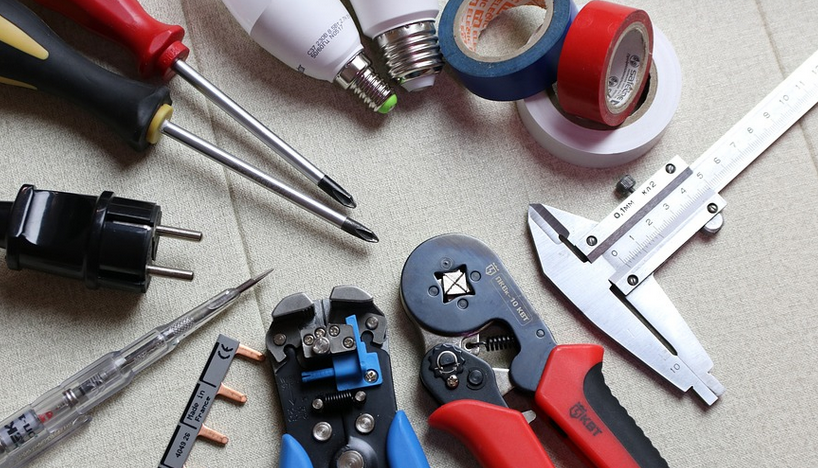
Understanding the Relationship Between Amps and Thickness
So, you’ve picked up your plasma cutter and are ready to tackle some metal projects! But hold on, before you start charging away, there’s a crucial but sometimes tricky element you need to understand: the relationship between amps (amperage) and thickness.
Think of it like this: for cutting through metal, we want to control how much power flows into the cut, which impacts the depth and quality of that cut. Amperage is essentially the amount of electrical current flowing through a circuit, directly influencing how much heat and energy are generated. A higher amperage translates to more power, meaning a stronger cut.
So, why do thickness play into the equation? Let’s say you want to cut a piece of metal with varying thicknesses. The material’s inherent resistance to cutting plays a role in determining how much current will be needed for an effective cut. The thicker the metal, the more resistance it offers, meaning you’ll need more amperage to melt through it.
Here’s where the “amps thickness chart” comes into play. This chart provides a helpful guide to understand the optimal amperage settings based on the specific material thickness you’re working with. It helps you calibrate your plasma cutter to effectively cut different thicknesses of metal without risking burns or damaging equipment.
What Are Plasma Cutters, and How Do They Work?
Imagine a tiny fiery sword, but instead of cutting through flesh, it slices through steel! Plasma cutters use the intense heat generated by an electric arc to cut through various materials.
A plasma torch is essentially a chamber filled with ionized gas (plasma) that creates a controlled stream of electrically charged particles. This plasma acts as a conduit for cutting through the metal, leaving behind clean, precise cuts.
The process starts by creating an electrical arc in the air within the torch head. The arc’s intense heat melts and vaporizes the metal at the cut line, allowing it to break apart smoothly. This high-speed cutting action ensures accurate and efficient cuts on various materials.
To ensure a successful cut, careful control of amperage and gas flow is crucial. Understanding this relationship between amps and thickness will optimize your plasma cutter’s performance for precise and consistent cuts.
The Importance of Amperage Chart
Imagine you have a sheet of metal that needs to be cut into two pieces. You need to choose the appropriate amperage setting on your plasma cutter to achieve a clean, accurate cut. If you set the amperage too low, you’ll struggle to melt through the metal and risk overheating it or damaging your equipment.
On the other hand, if you use an excessively high amperage, you might overheat the material, resulting in uneven cuts and even potential damage to the torch itself.
An amp thickness chart is like a map for your plasma cutter’s journey through different thicknesses of metal. It helps you find the optimal amperage setting based on the specific thickness you’re working with.
These charts are often found in user manuals or offered by manufacturers as downloadable resources. They provide valuable insights into the relationship between amps and various metal thicknesses, ensuring efficient cuts and reducing the risk of damage to your equipment.
Why It Matters:
Choosing the correct amperage is essential for a successful plasma cut and prevents unwanted issues. Using too low an amperage will lead to sluggish cuts, potentially causing burrs or incomplete cuts. Using too high an amperage can result in uneven cuts and even material deformation.
Using an amperage chart ensures you achieve the desired thickness of the cut with precision, leading to a better finish and more efficient cutting time.
Making The Most of Your Plasma Cutter
Remember, plasma cutters are powerful tools, but understanding their limitations is key to using them safely and effectively. The amperage chart plays a crucial role in unlocking the true potential of your plasma cutter.
With the right knowledge and practice, you can confidently tackle any project, from crafting intricate metal designs to building sturdy structures. Just remember, careful planning and precise control over your plasma cutter’s settings are what make the difference between a good cut and a masterpiece.
Happy cutting!