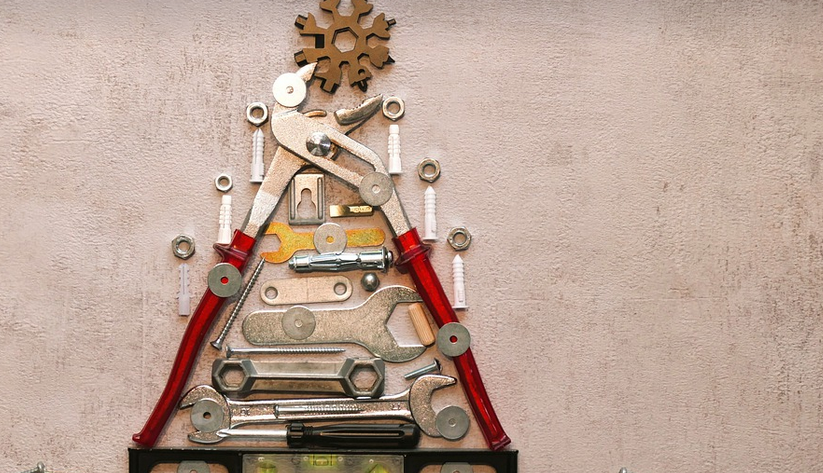
Streamlining Metalworking with Cutting-Edge Technology
Metal fabrication has long been a cornerstone of countless industries, from construction to aerospace, automotive, and even artistic endeavors. The need for precise, efficient, and high-speed cutting methods has driven the development of innovative technologies, and at the forefront of this revolution is the heavy-duty power systems plasma cutter.
These powerful machines have become a transformative force in metal fabrication due to their ability to cut through various metals with exceptional speed and precision. Unlike traditional methods like oxyacetylene torches or laser cutting, which often rely on high heat or focused beams, plasma cutters utilize the raw power of a pressurized gas jet to generate plasma.
But what exactly is plasma, and how does it work? Plasma is essentially an ionized gas—free-floating electrons and ions that have been stripped from their atoms. This highly energized state creates a unique cutting capability. Imagine a superheated plasma stream, capable of melting through metal like butter! The process works by applying a high voltage to the gases inside the machine, generating intense heat.
This intense heat vaporizes and melts the metal, creating clean cuts with minimal material loss. The molten metal then cools down and solidifies, leaving behind a precise cut without any significant burrs or jagged edges.
Imagine building an intricate steel frame for a construction project, or joining different sections of metal together effortlessly. With plasma cutters, the possibilities are endless. They can handle thick-gauge metals like stainless steel, aluminum, and even heavy-duty ferrous materials with ease. This versatility opens up new avenues for complex fabrication projects.
Heavy-duty power systems plasma cutters come in various forms, each designed to cater to specific needs. They range from compact portable units suitable for smaller jobs and hobbyist tasks, to industrial-scale machines capable of handling massive metalwork projects with precision and speed.
One aspect that makes them stand out is the inherent safety features. These machines are equipped with advanced protections to prevent overheating, sparks, or other potential hazards. Safety features like automatic shut-off mechanisms, interlocks for controlled operation, and dust suppression systems come standard to ensure operator safety and a clean working environment.
The benefits of using heavy-duty power systems plasma cutters are manifold. This advanced technology offers numerous advantages over traditional methods. They deliver higher cutting speeds than conventional tools, resulting in significant time savings and increased productivity.
Another crucial advantage is precision accuracy. The controlled flow of the plasma arc allows for highly accurate cuts, eliminating uneven edges or jagged lines that can occur with other processes. Plasma cutters also offer a cleaner cut compared to traditional methods, reducing post-processing needs such as grinding and sanding.
The use of power systems in these machines ensures consistent cutting results even on thicker metals. These systems provide the necessary power to generate the required plasma arc, leading to smoother cuts and reduced material waste.
Beyond efficiency and precision, plasma cutters are also revolutionizing metal fabrication processes by reducing environmental impact. With lower energy consumption and minimal smoke or fumes, they offer a sustainable solution for industrial-scale operations. The reduction in waste materials further contributes to a more eco-conscious approach to manufacturing.
The versatility of plasma cutting technology extends beyond the realm of traditional machining. It has opened doors for new creative avenues like artistic metalwork or even architectural installations, where precision and artistry converge.
Let me know if you’d like to explore any specific aspect of heavy-duty power systems plasma cutters in more detail!