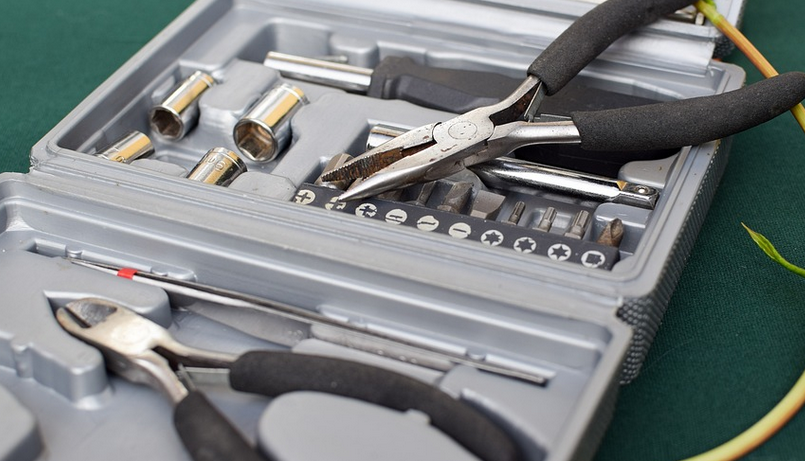
A Handy Guide for Industry Professionals
In the realm of industrial processes, especially when it comes to handling fluids like liquids or gases, knowing your fittings is crucial. And one such fitting that’s gained a lot of popularity and prominence is the Tri Clamp Fitting.
But what exactly is a Tri Clamp Fitting? Well, imagine this: you have a pipe system, perhaps a brewery brewing beer or a wastewater treatment plant separating sludge, and you need to connect different sections. You need a secure way to join those pipes together – that’s where the Tri Clamp comes in.
The beauty of Tri Clamps lies in their versatility. They’re renowned for their ability to be easily assembled and disassembled, making them ideal for quick repairs or even simple adjustments in the field. Plus, they allow for a wide range of pipe sizes and connections, offering a solution that suits various applications.
But let’s delve deeper into the world of Tri Clamp Fittings. You might wonder about their compatibility with different materials and how to determine the optimal size for your specific need. Let’s explore some key factors behind choosing the right fitting.
The Importance of Size
Before we dive into the nitty-gritty, let’s talk about just why size is so crucial in this context. It all boils down to compatibility and functionality.
Consider a scenario – you’re designing a system for air filtration, where precise control over fluid flow is paramount. If you choose the wrong Tri Clamp size, it can lead to leaks, inefficiencies, or even potential safety hazards. The right size ensures smooth and trouble-free operation.
Tri Clamps are designed with specific size ranges in mind. Each fitting comes with a defined inner diameter, which is crucial for ensuring secure connections and optimal flow.
To understand the importance of size, let’s consider some factors that impact selection –
**1. Type of Fluid:** The fluid you’re handling plays a vital role in determining the correct Tri Clamp size. * **Liquids:** For liquids like water or chemicals, the flow rate and viscosity (resistance to flow) need to be considered. * *Higher viscosity fluids require larger Tri Clamps for efficient movement.* * **Gases:** Gases like air or nitrogen require smaller diameter fittings because they don’t experience significant pressure drop when flowing through them. * *Note: Safety is paramount when handling gases. Ensure proper ventilation and appropriate PPE (Personal Protective Equipment) to avoid any accidents.* **2. Flow Rate:** The amount of fluid passing through the fitting needs to be factored in. A higher flow rate demands larger Tri Clamps for better efficiency. * **Example:** Imagine a system with a pump, where water is being drawn from a well and transported to a storage tank – high flow rates would necessitate a bigger Tri Clamp size to handle the volume of water efficiently. **3. Pressure:** The pressure inside the system also plays a significant role in determining the correct fitting size. High-pressure systems require larger Tri Clamps to withstand the force exerted on them. * **Example:** A high-pressure boiler requires specialized Tri Clamps designed for higher pressures, ensuring safety and preventing leaks. **4. Material Compatibility:** The materials of your pipes play a role in choosing the right Tri Clamp size. Ensure compatibility between the fitting material and the pipe material to avoid corrosion or other damage. * **Example:** A system using stainless steel pipes would need Tri Clamps made from stainless steel to prevent wear and tear, especially under high-pressure conditions. **5. Regulatory Compliance:** Some industries have strict regulations regarding pipe fittings. To ensure compliance with these standards, it’s crucial to use specific Tri Clamp sizes that meet those requirements, maintaining a safe and legal operation. * **Example:** In the chemical industry, certain chemicals are strictly regulated, requiring specific Tri Clamps for compatibility and safety measures
Understanding the factors mentioned above will help you choose the right size. However, if you’re unsure about your specific needs or require expert advice, reach out to a qualified industrial engineer or fitting specialist. They possess valuable experience and knowledge that can guide your decision and ensure your system runs smoothly.
Choosing the correct Tri Clamp size is essential for ensuring efficient operation, safety, and compliance with regulations. By considering these factors meticulously, you can confidently navigate the world of Tri Clamps and build successful systems in 2025 and beyond.